With increasing demand for composite materials on the industrial scale, more effort is put in seeking optimized sets of parameters (speed, temperature, pressure, …) for the Automated Fiber Placement (AFP) process that ensure a fast and reliable process with aerospace grade output. One key aspect for reaching this goal is to better understand the temperature distribution within the substrate during the AFP process.
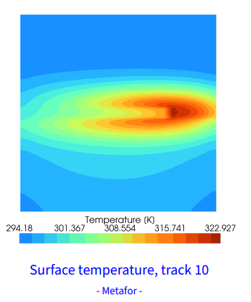
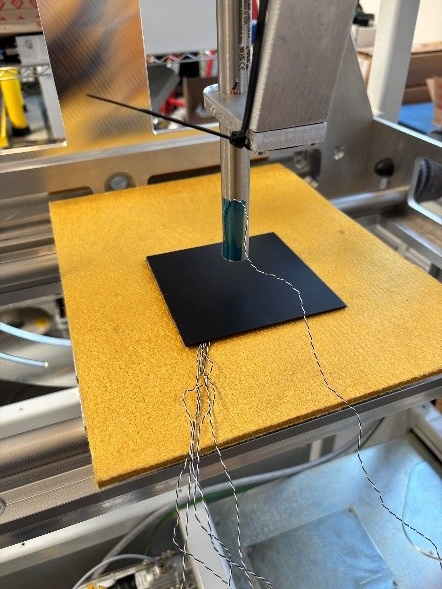
In this context, through-thickness and surface temperature distributions are experimentally and numerically investigated under various heating sources (hot gaz torch, pulse light, laser). Square sample parts are laid up on AFP equipment with either unidirectional or symmetric stacking sequence
Through-thickness temperature is measured throughout the process by the means of thermocouples, embedded in the substrate and equally spaced as to form a grid. Surface temperature is measured at the vicinity of the nip point by using infrared thermal camera. A 3D transient thermal finite element model is developed, using particle finite element method (PFEM) for the modeling of hot gas torch. After a correlation phase, results from the 3D model are used to predict thermal behavior of the composite part.
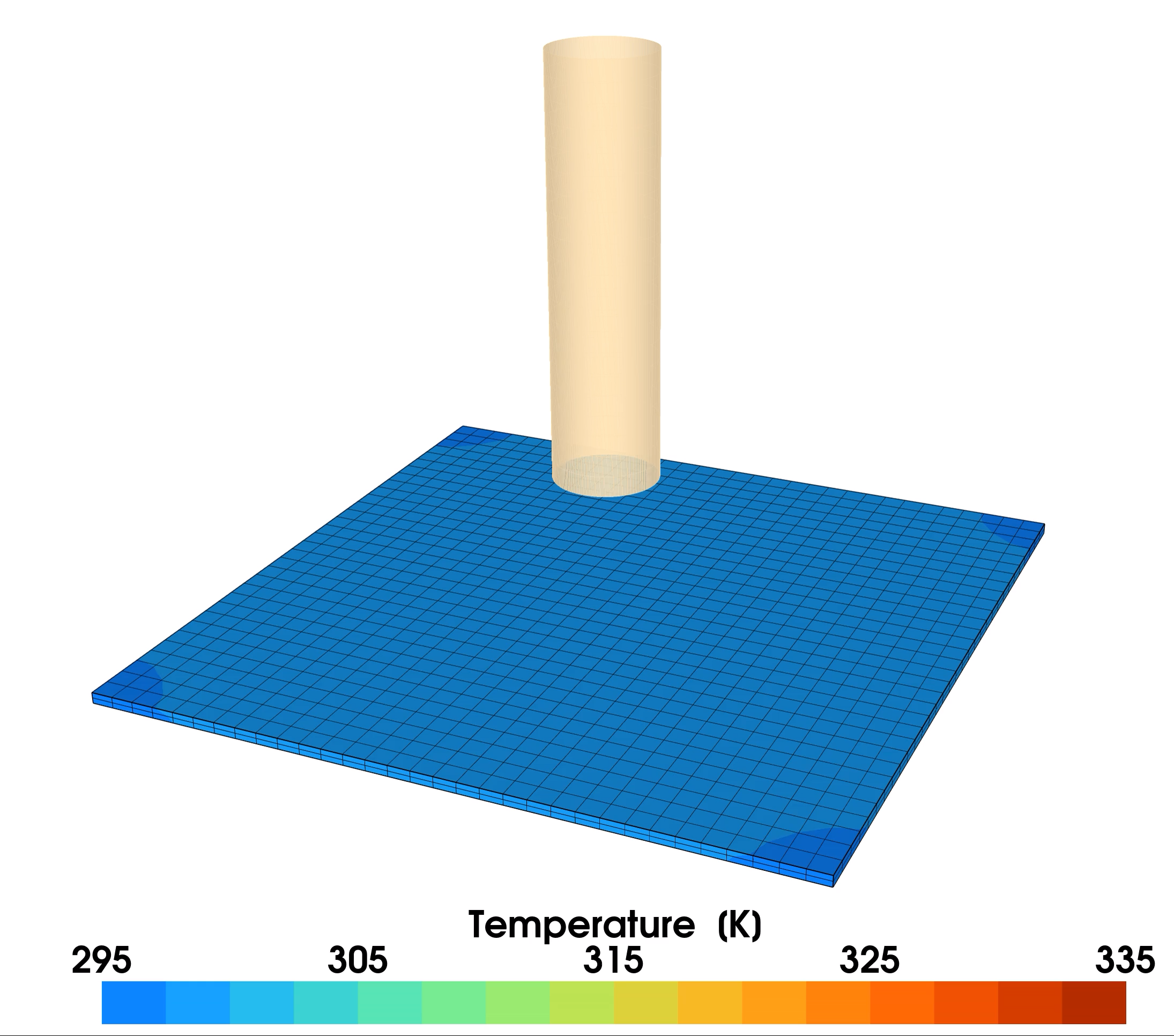
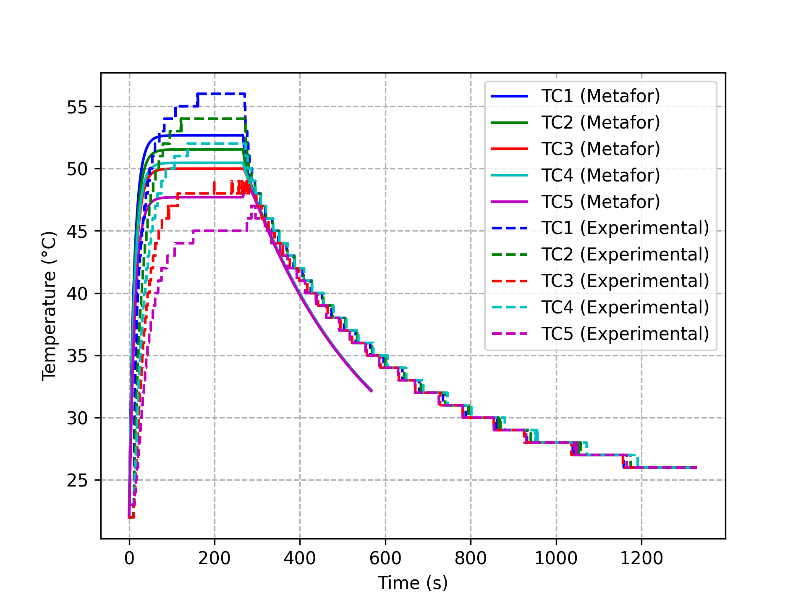
For detailed technical specifications of all our machines, please refer to the catalog attached below.