The ambition of the ESI-F35 project, started in 2022, is to propose a module to complement existing calculation codes that simulate the paths of the fiber placement head and predict the quality of the associated process, and to work on improving the performance of thermoplastic materials by in-situ consolidation using alternative heating systems such as pulsed light or laser. This research involves the development of highly instrumented test benches for material characterization, and the manufacture of a high-performance fiber placement machine using dual-laser system.
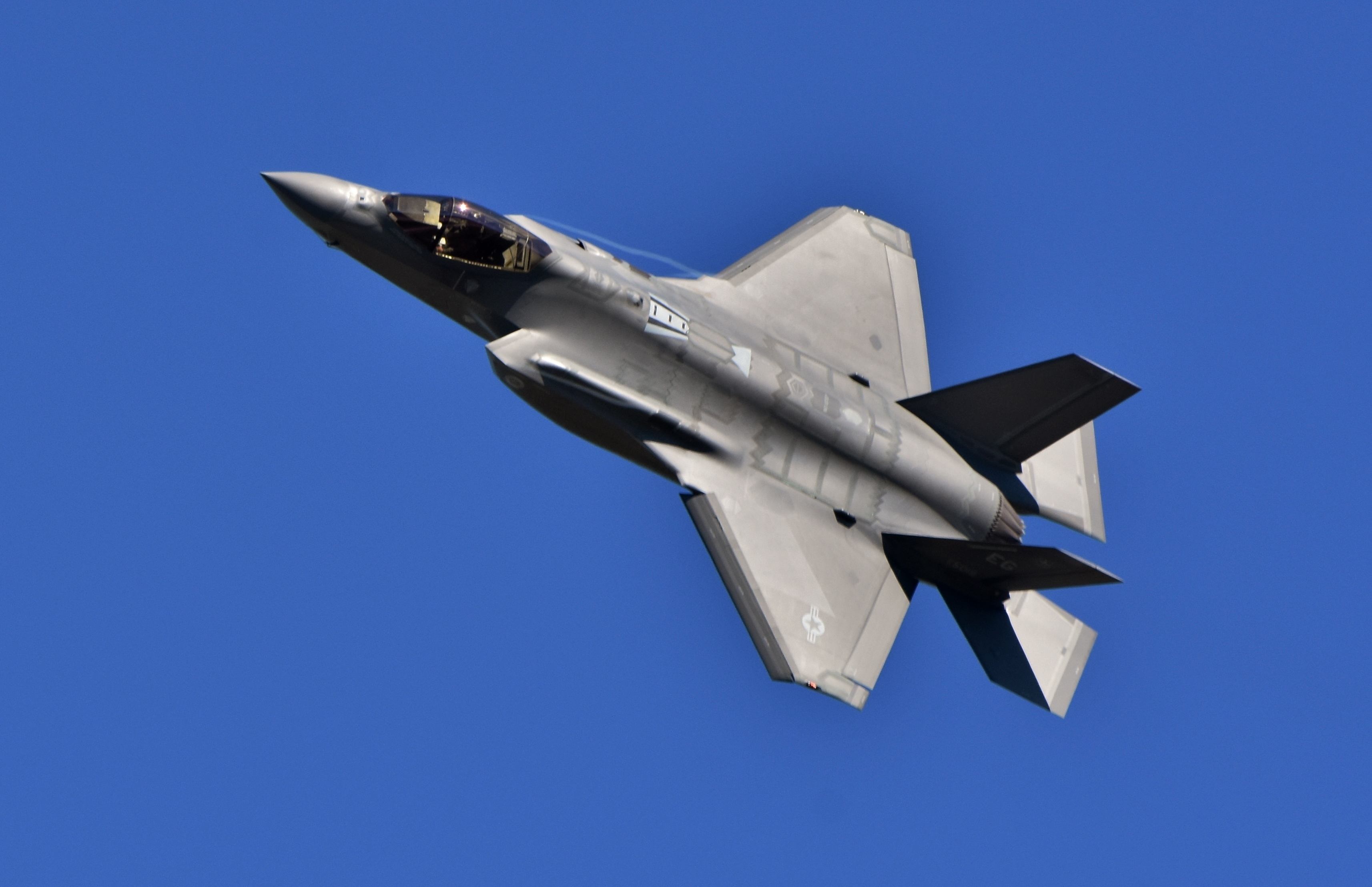
The ESI-F35 project successfully reached its first milestone. Coexpair Dynamics completed the design, development and manufacture of a unique Thermoplastic Automated Fiber Placement automation equipment for Syensqo, supplier of advanced composite materials, as part of the ESI-F35 project of Essential Security Interests for Belgium aligned
with Lockheed Martin needs.
Project
ESI-F35 – Advanced Thermo-Plastics Manufacturing with consolidation in-situ for high performance composite aero structures
Project overview
4 partners, Coexpair Dynamics & Syensqo, University of Liège, Lockheed Martin €7.6 million budget
Programme
Project funded by Wallonia an the Belgian Royal Higher Institute for Defence (RHID)
Project Website
(ongoing)
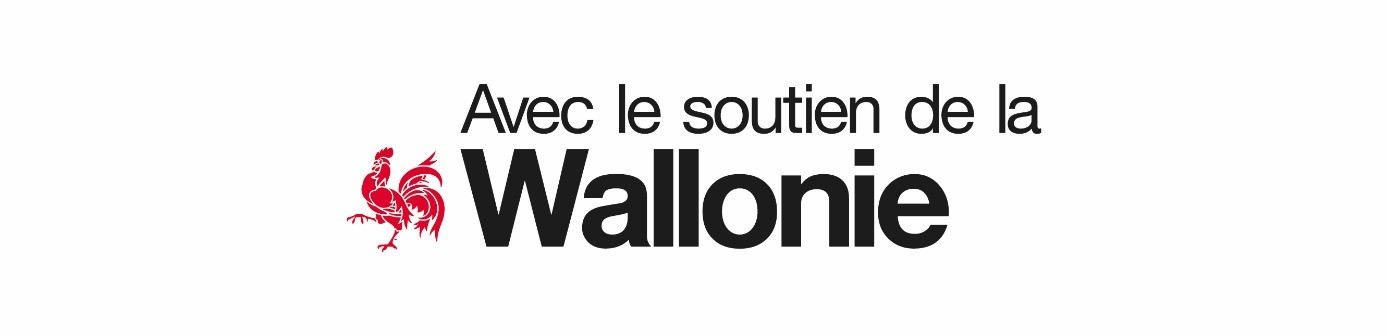
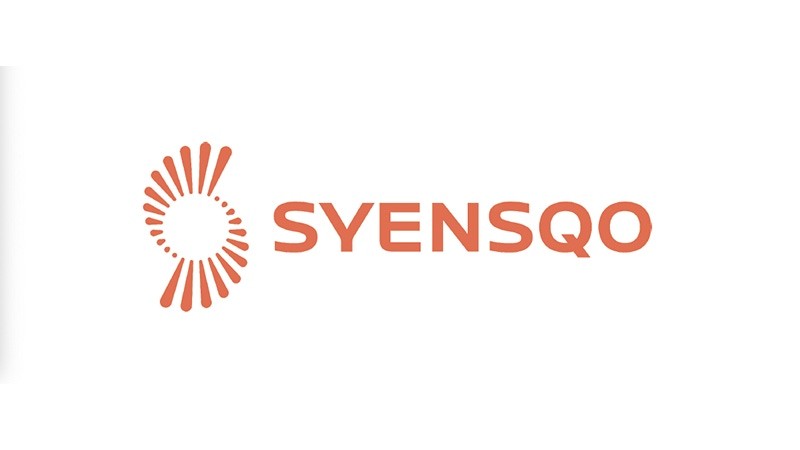
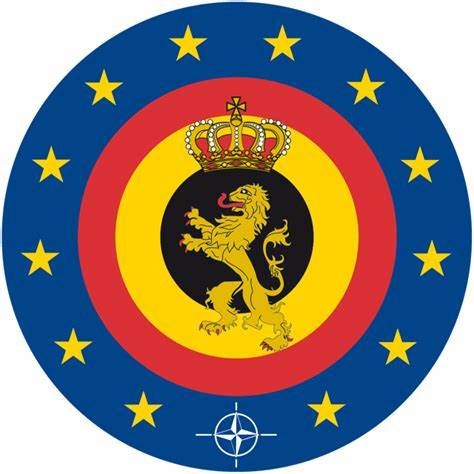
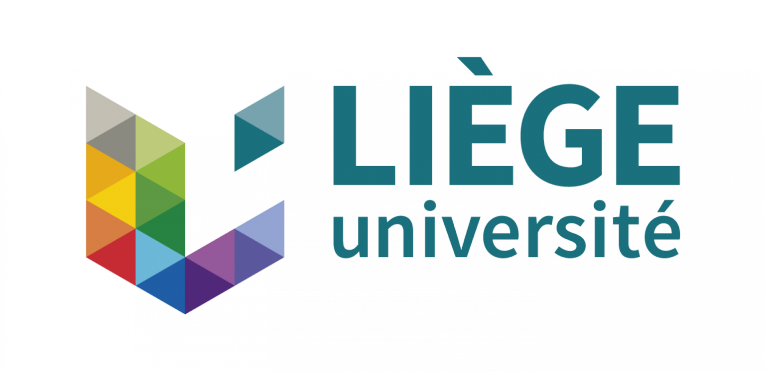
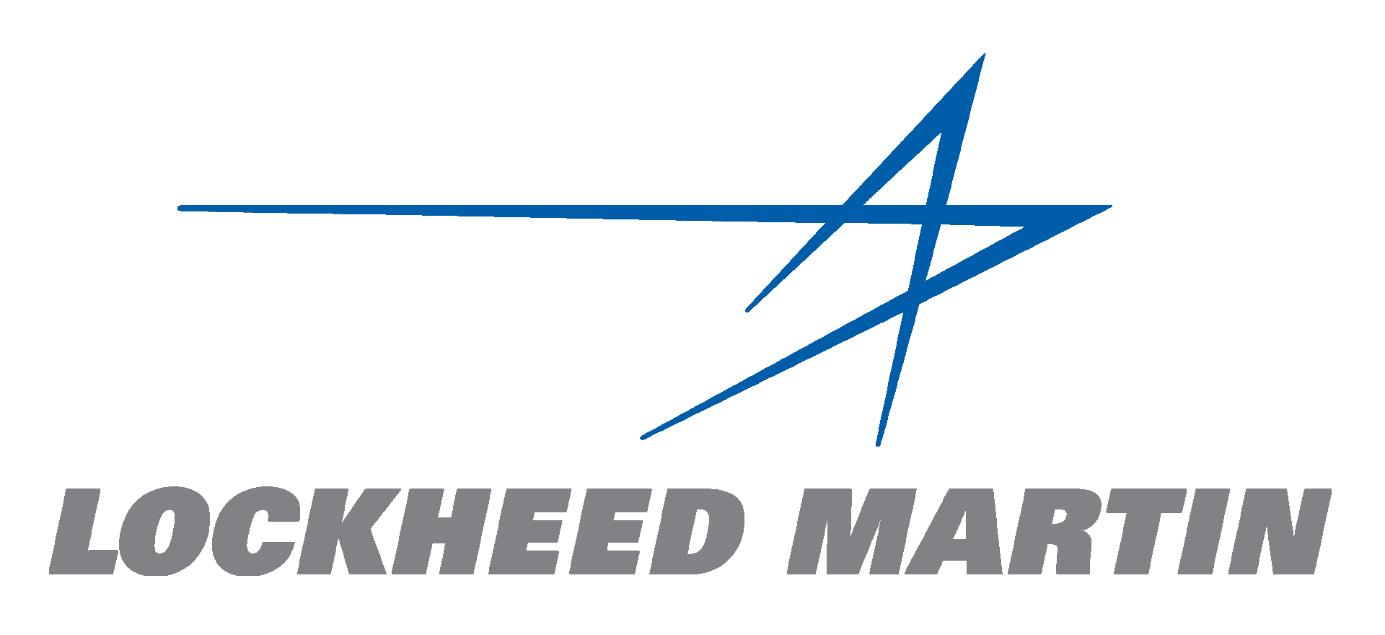
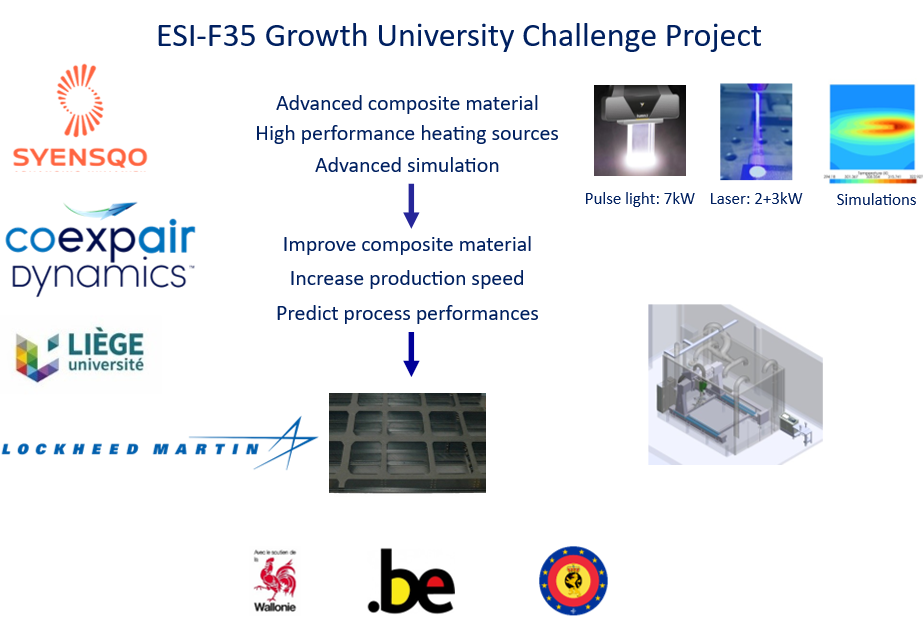
The cutting-edge platform, developed by Coexpair Dynamics [Namur, BE] in partnership with Pegard Productics for the gantry and Siemens for the control
systems, integrates the most advanced thermoplastic fiber placement head developed by Trelleborg Sealing Solutions Albany [USA]. This equipment will be
an enabler for the adoption of thermoplastic composites in Aerospace by using Syensqo’s advanced composites in an automated in-situ consolidation process. Indeed, thanks to its unique dual laser heating system, high deposition speed and optimal processing parameters can be achieved.
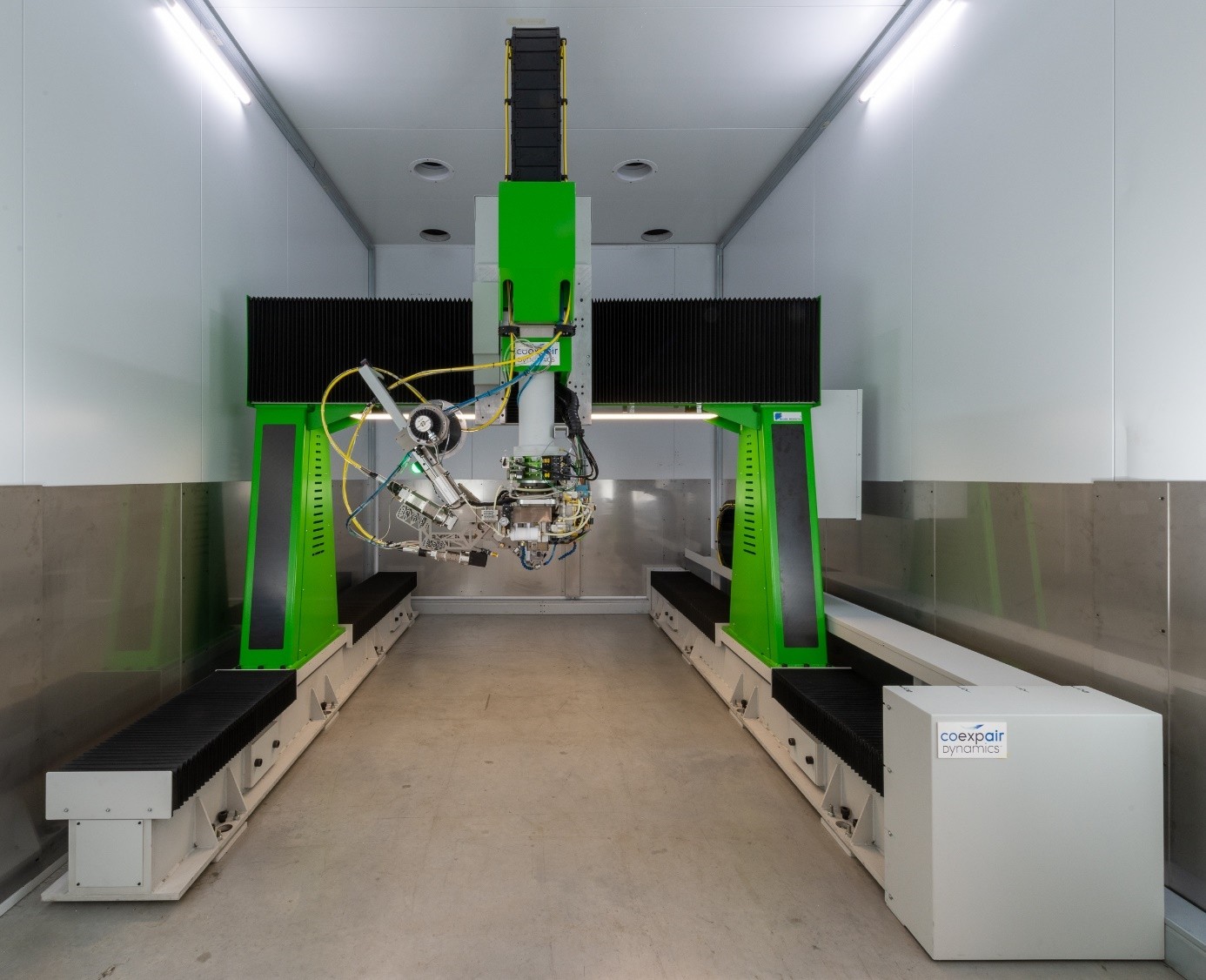
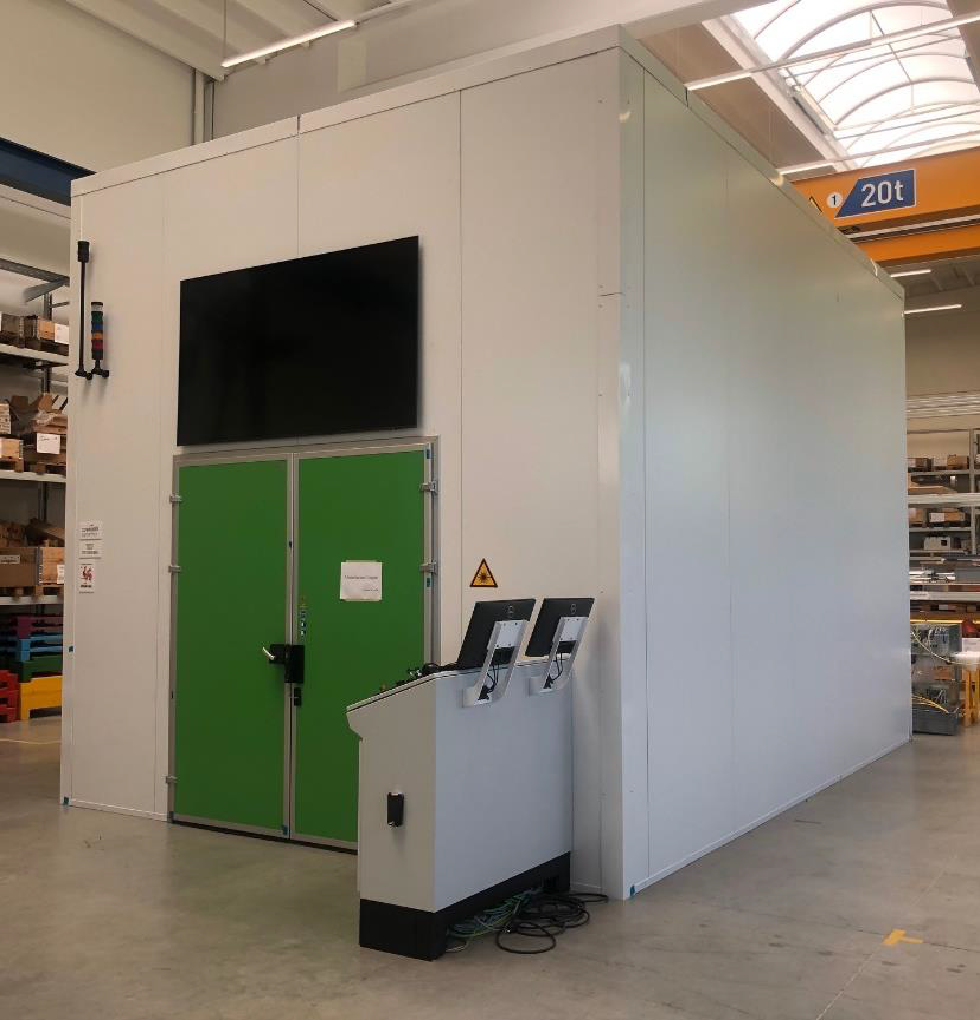
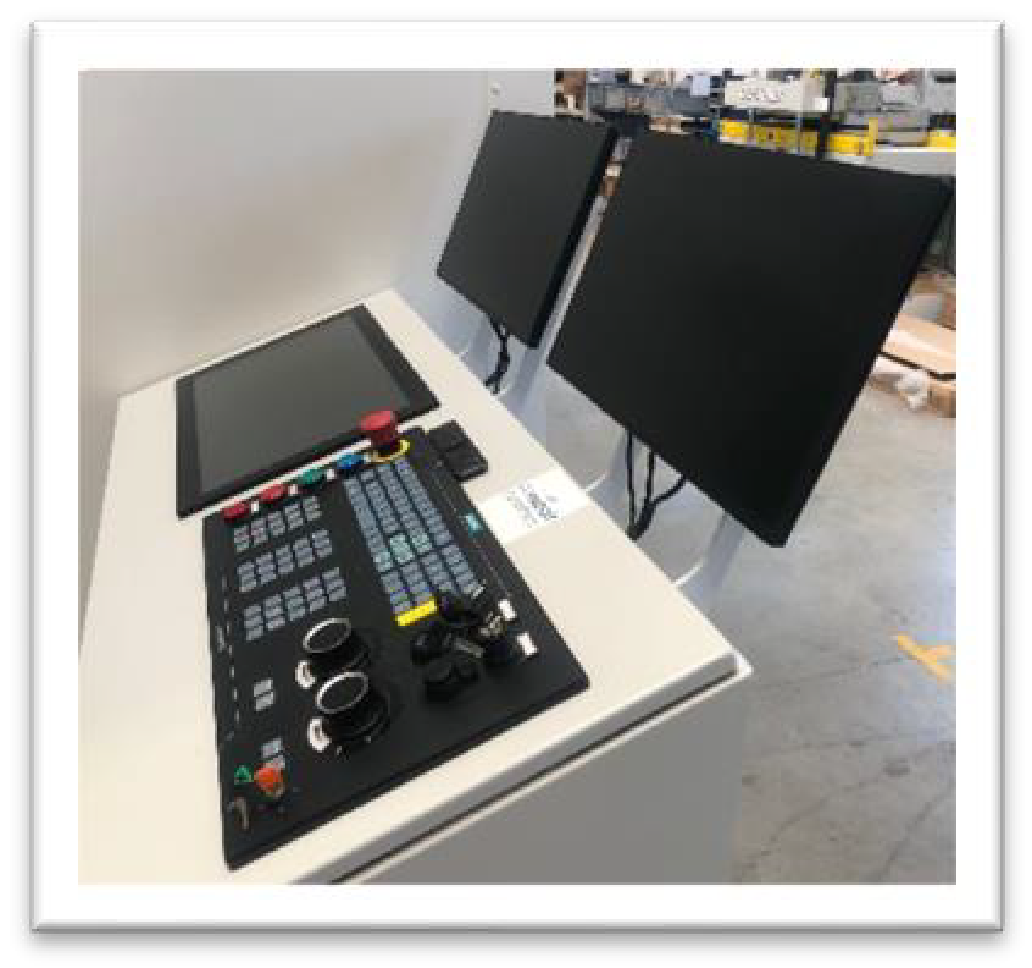
The ESI-F35 partnership, led by Coexpair Dynamics, brings together all the necessary expertise for the success of this project. Syensqo [headquartered in
Brussels and with a global footprint], through the supply of its aerospace grades of thermoplastic composites, and its advanced application engineering
expertise has been able to advise on the requirements for the equipment to best perform when combined with its proprietary materials. The Aerospace and Mechanics Department of ULiège is working on advanced local numerical simulation of the deposition process for the purpose of direct correlation with the thermal tests carried out on the Coexpair Dynamics test benches. The kinematic axes of the Coexpair Dynamics machines are equipped with the
Sinumerik One control system from Siemens, which provides continuous advanced technical support to Coexpair Dynamics for the development of this equipment. Lockheed Martin also supports the ESI/F35 program with periodic visits on site. Pegard Productics, an heir to CNC machines in Wallonia, based in Andenne, provides an ultra-precise gantry solution (with “no size” limit). The American company Trelleborg Sealing Solutions Albany, formerly Automated Dynamics, has been a global leader in automated fiber placement for over 30 years and is Coexpair Dynamics' preferred partner for placement heads.